The manufacturing industry, along with most others, is undergoing significant change, driven by a suite of technologies coined as Industry 4.0.
This new era is revolutionising traditional manufacturing practices.
In this briefing, we delve into:
- The core components of Industry 4.0
- Its benefits
- Real-world examples of its implementation
The core components of industry 4.0
1. Cyber-physical systems (CPS):These are systems where physical processes are monitored and controlled by computer-based algorithms, tightly integrated with the internet and its users. CPS enables real-time data collection and analysis, allowing manufacturers to make informed decisions and optimise operations.
2. Internet of things (IoT): IoT involves connecting machines, devices, and sensors to the internet, facilitating seamless communication and data exchange. In manufacturing, IoT is used to monitor equipment health, track inventory, and streamline supply chains.
3. Cloud computing: Cloud-based platforms provide scalable and flexible infrastructure for storing and processing vast amounts of data. They enable manufacturers to access real-time data from anywhere, fostering collaboration and reducing IT costs.
4. Artificial intelligence (AI) and machine learning (ML): AI and ML algorithms analyse data to predict trends, identify anomalies, and optimise processes. In manufacturing, these technologies are used for predictive maintenance, quality control, and demand forecasting.
5. Big data analytics: The ability to analyse large datasets allows manufacturers to gain insights into their operations, identify inefficiencies, and make data-driven decisions. Big data analytics helps in improving product quality and reducing production costs.
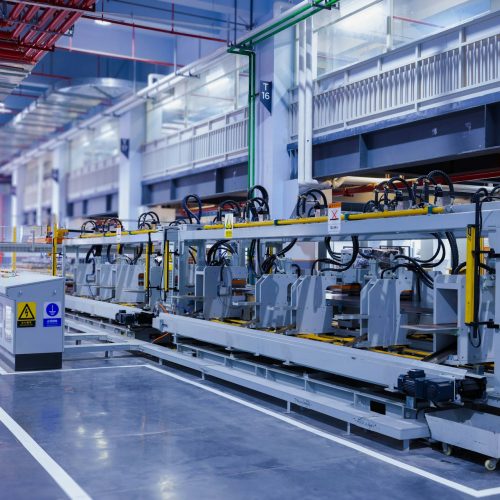
Benefits of industry 4.0
Increased efficiency: Real-time monitoring and automation can reduce downtime, optimise resource utilisation, and streamline production processes.
More visibility and control: The ability to collect and analyse greater volumes of data from the shop floor, enables management to keep a closer eye on what is happening within the organisation.
Reduced risk: With increased visibility and greater monitoring comes lower risk.
Improved quality: Advanced analytics and machine learning can enhance quality control by detecting defects early and ensuring consistency.
Flexibility and customisation: Smart manufacturing systems can quickly adapt to changing demands, allowing for greater customisation and shorter lead times.
Cost reduction: Predictive maintenance and optimised operations reduce maintenance costs and minimise waste, leading to significant cost savings.
Enhanced collaboration: Cloud computing and IoT enable seamless communication and collaboration across different locations and departments.
Real-world examples of industry 4.0
1. Siemens digital factory: Siemens has been at the forefront of adopting Industry 4.0. Its Amberg Electronics Plant in Germany is a prime example. The factory uses a combination of IoT, AI, and robotics to achieve nearly complete automation, with machines handling 75% of the production process. 16 million SIMATIC products are produced annually, with a defect rate of only 0.001%.
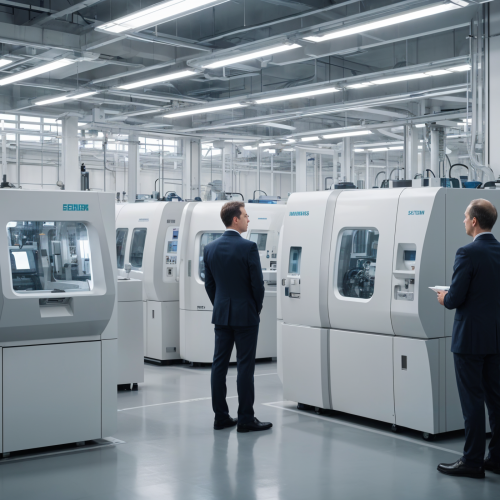
2. General electric (GE) brilliant factories: GE has implemented Industry 4.0 principles in its Brilliant Factories initiative. These factories use advanced analytics and IoT to monitor equipment performance and optimise production. In a number of GE factories, predictive analytics has successfully reduced unplanned downtime, leading to significant cost savings and productivity improvements.
3. BMW’s smart factory: BMW’s smart factories, such as Dingolfing, Germany, integrates IoT, robotics, and AI to streamline vehicle production. Factories use autonomous guided vehicles (AGVs) to transport materials and AI-powered quality control systems to inspect components. It is believed that these integrations have resulted in a material increase in production efficiency and a significant reduction in logistics costs .
4. Foxconn’s automated manufacturing: Foxconn, a leading electronics manufacturer, has embraced Industry 4.0 by deploying over 40,000 robots in its factories. These robots handle repetitive tasks, improving efficiency and reducing labour costs. In addition, Foxconn uses IoT and big data analytics to monitor equipment health and optimise production lines.
Conclusion
Industry 4.0 is not just a buzzword but a force that is reshaping the manufacturing landscape. By leveraging cyber-physical systems, IoT, cloud computing, AI, and big data analytics, manufacturers can achieve greater levels of efficiency, quality, and flexibility.
Real-world examples from industry leaders like Siemens, GE, BMW, and Foxconn demonstrate the tangible benefits of adopting Industry 4.0 technologies. But Industry 4.0 isn’t just for the world’s largest manufacturers. Manufacturing firms of all sizes are digitally transforming their processes to solve their greatest business challenges and improve efficiency.
As the manufacturing sector continues to evolve, embracing digital transformation will be crucial for staying competitive and driving future growth.